Chuyển đổi kỹ thuật số, được thiết lập trong sự tăng trưởng của IoT công nghiệp, và đây là một practice khá trừu tượng. Nó không phải là một loại dự án ngắn hạn. Nó đòi hỏi tất cả các bên hợp tác để ảnh hưởng đến sự thay đổi và tái phát minh, nắm bắt văn hóa kinh doanh và thực tiễn kinh doanh để tạo ra những giá trị mới cho doanh nghiệp.
Điều quan trọng, doanh nghiệp cũng cần xem xét các chi tiết nhỏ về thuật toán của nhiều chức năng doanh nghiệp và khi chúng tác động đến chuỗi cung ứng tiến và lùi. Bạn có thể có được giải pháp on-premise từ một trong những nhà cung cấp cloud IoT, nhưng nó chỉ dành cho một bộ phận cụ thể nào đó của thiết bị và đó không phải là cách để thu thập dữ liệu toàn bộ mà bất kỳ dây chuyền sản xuất nào đang hoạt động.
Để có được một kết quả có ý nghĩa, bạn phải tích hợp và triển khai trên nhiều hệ thống khác nhau – để đưa ra bất kỳ loại quyết định kinh doanh nào. Và đây không phải là một giải pháp đóng gói sẵn. Có nhiều nhà cung cấp khác nhau tạo nên dây chuyền sản xuất. Bạn có thể có 10 thiết bị khác nhau được sản xuất bởi 10 công ty khác nhau, với 10 nhà cung cấp cloud khác nhau thu thập dữ liệu từ họ.
Tuy nhiên chuyển đổi sản xuất không phải là khó. Nó chỉ cần lập kế hoạch và kiên nhẫn. Bước đầu tiên, chỉ để đạt được khả năng hiển thị trực quan hoá dữ liệu sản xuất, có thể mang lại phần thưởng đáng kể.
Công ty công nghệ sinh học Thụy Sĩ Lonza – với 112 và 15.000 nhân viên ở Châu Âu, Bắc Mỹ và Nam Á – mới phát hiện ra điều này. Từ năm 2017, bộ phận Thành phần Đặc biệt Lonza (LSI), sản xuất mọi thứ từ dầu gội chống gàu đến sơn phủ ăn mòn, đã tìm cách cung cấp dữ liệu sản xuất từ các nhà máy của mình tại trung tâm data science trung tâm ở Visp, Thụy Sĩ.
LSI đã xem xét các cơ sở sản xuất của mình tại thời điểm đó, đánh giá từng cơ sở trên hệ thống đèn để xử lý dữ liệu: hầu hết các site đều được bật đèn đỏ ngưng sử dụng giấy; một số ít đã chuyển sang màu hổ phách để ghi dữ liệu quá trình trong cơ sở dữ liệu chuỗi thời gian của ‘historian’; chỉ có hai trạm là sử dụng công cụ dữ liệu chính thức và bảng điều khiển. Và trước đó họ làm phân tích dữ liệu nâng cao.
Mạng lưới sản xuất LSI được trang bị 150.000 cảm biến, cung cấp khả năng kiểm soát các quy trình sản xuất của nó. Bước đầu tiên chỉ là đưa dữ liệu từ vô số các cảm biến và hệ thống của nó vào một hệ thống duy nhất, giám đốc công nghệ vận hành toàn cầu tại Lonza nói.
Chúng tôi có rất nhiều hệ thống ở cấp local . Giai đoạn đầu tiên là kết nối với hệ thống, và giai đoạn thứ hai là trực quan hóa dữ liệu trong đó. Đó là những phân tích hầu như không phức tạp, ông nói tại nhánh châu Âu của PI World của OSIsoft ở cùng nhau tại Gothenburg vào đầu tháng này, ở Thụy Điển.
LSI đã triển khai một hệ thống quản lý dữ liệu thống nhất dựa trên cơ sở hạ tầng PI của OSIsoft. PI được thiết lập tốt giữa các nhà công nghiệp như một kho lưu trữ dữ liệu vận hành và một nền tảng cơ sở để hợp nhất nhiều nguồn dữ liệu.
Công ty cũng đã hợp tác với Microsoft để lưu trữ dữ liệu trên cloud và các công cụ IoT và nhà cung cấp IoT và AI công nghiệp có trụ sở tại Seattle, Seeq (cùng với địa chỉ với PI World), nhắm đến các doanh nghiệp ‘nghèo thông tin’ trong sản xuất dạng quy trình, để cung cấp da Dashboardtrên đầu và các công cụ AI đi kèm với nó.
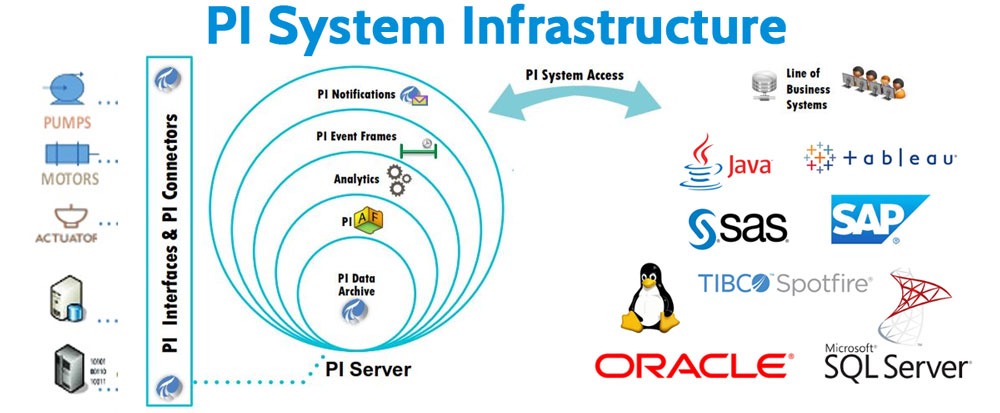
Nó sẽ chỉ chuyển sang mô hình hóa và thực hiện phân tích để kiểm soát quá trình sau khi hoàn thành các nhiệm vụ ban đầu này.Phần mềm Chúng tôi muốn tập trung các hoạt động và tài nguyên của chúng tôi vào các giai đoạn đầu tiên này, để cung cấp cơ sở hạ tầng để cho phép nhân viên vận hành hiểu rõ hơn về dữ liệu. Chúng tôi đang xây dựng các giải pháp riêng cho các nhà máy đơn lẻ, , Merz nói.
Công việc sẽ không được vội vàng, và nhân viên sản xuất sẽ được tham gia ở mọi bước. Đây là một tầm nhìn, bây giờ, anh ấy nói về kế hoạch tổng thể của công ty, để đi đến sản xuất có hỗ trợ AI đầy tham vọng hơn. Nhưng động thái đầu tiên của nó để hợp nhất dữ liệu sản xuất toàn cầu của nó đã bị áp đảo, ông nói thêm.
Cho đến nay, LSI có 400 người dùng trong 10 cơ sở trên hệ thống Seeq, chạy trên thiết bị PI. Khoảng 150 quy trình đang được theo dõi và tối ưu hóa thông qua DashboardSeeq.
Merz có một tính toán rằng nhân viên đang tiết kiệm 15.000 giờ mỗi năm với Dashboardtrực quan hóa dữ liệu của Seeq, so với thời gian họ dành mỗi buổi sáng để khám phá cùng một thông tin, chủ yếu về hoạt động vào ban đêm của nhà máy.
Hơn thế nữa, hệ thống đã thay đổi cách thức kinh doanh kết hợp với nhau. Đây không chỉ là sản xuất; nó thực sự đi vào các bộ phận khác nhau. Đó là một công cụ ra quyết định, một giải pháp tìm kiếm cùng nhau. Bởi vì nhân viên sản xuất sẽ mở màn hình Seeq vào buổi sáng và thảo luận trực tiếp về dữ liệu và thông tin hiện có, anh nói.
Họ không cần phải quay lại hệ thống kiểm soát phân tán ban đầu và sau đó tạo bản sao. Mọi người đều nói cùng một ngôn ngữ. Hệ thống đang thay đổi cách chúng ta nhìn vào dữ liệu và cách chúng ta thảo luận các vấn đề trong sản xuất.
Nó sẽ để chúng ta ở đâu? Các ngành công nghiệp đang sử dụng AI để tạo hiệu ứng tuyệt vời trên dây chuyền sản xuất. Nhưng những ví dụ như vậy vẫn là ngoại lệ, và chúng có xu hướng hoạt động – tuy nhiên cũng tốt – trong sự cô lập. Có thể đạt được nhiều lợi ích chuyển đổi hơn bằng cách triển khai các giải pháp phân tích đơn giản hơn – thường là AI – ở quy mô lớn hơn, bên trong các mạng của nhà máy và trên toàn bộ chuỗi cung ứng.
Trước đây Vào tháng 7 nằm 2019, Công ty Lonza có trụ sở tại Thụy Sĩ, được thành lập vào năm 1897 với khoảng 7.500 nhân viên, đã chọn phần mềm Hệ thống thực thi sản xuất PharmaSuite (MES) của Rockwell Automation để số hóa các hoạt động trong môi trường sản xuất của họ. Cụ thể, giải pháp được thiết kế để giúp tránh sự gián đoạn trong thời gian khối lượng lớn của các đơn đặt hàng đúng lúc cho sản xuất theo yêu cầu, mở ra một kỷ nguyên mới về hiệu quả hoạt động.
Lonza sẽ sử dụng phần mềm PharmaSuite MES, cùng với phần mềm FactoryTalk InnovationSuite để theo dõi sản phẩm tốt hơn đến từng hộp đựng viên nang và hiểu rõ hơn về hiệu suất và sản xuất. Một sự tách biệt giữa SAP và PharmaSuite MES cũng sẽ giúp tránh sự gián đoạn trong trường hợp tắt kế hoạch tài nguyên doanh nghiệp toàn cầu hoặc bảo trì cần thiết bằng cách thực thi quy trình công việc và thu thập thông tin cần thiết.
Nguồn : Enterprise IoT Insights.