Hệ thống MRP là gì?
Hệ thống MRP là phần mềm sản xuất trung tâm mà các công ty sản xuất sử dụng để quản lý, tối ưu hóa, lên lịch và tự động hóa các phần lớn của quy trình sản xuất. Phần mềm này tích hợp các khía cạnh chính của sản xuất vào một bộ năng suất duy nhất, bao gồm sản xuất, quản lý hàng tồn kho, quản lý đơn hàng, lập kế hoạch mua sắm, lập kế hoạch sản xuất và nhiều chức năng khác.
Ở dạng ban đầu, MRP đề cập đến việc lập kế hoạch yêu cầu vật liệu. Thuật ngữ này được đặt ra cách đây khoảng 60 năm và tạo thành một kỹ thuật mang tính cách mạng khi đó để quản lý hàng tồn kho và lập lịch trình cho các quy trình sản xuất.
Ngày nay, lập kế hoạch yêu cầu vật liệu được gọi là MRP I và mặc dù nó đặt “MRP” ban đầu trong “hệ thống MRP”, các hệ thống MRP hiện đại thực sự sử dụng phương pháp lập kế hoạch sản xuất tiên tiến hơn nhiều gọi là lập kế hoạch nguồn lực sản xuất, còn được gọi là MRP II .
Ưu điểm của các hệ thống hiện đại này so với lập lịch trình thủ công hoặc các công cụ lập kế hoạch cơ bản hơn là rất lớn. Được tổng hợp thông qua cách tiếp cận có hệ thống để quản lý một doanh nghiệp sản xuất, chúng chuyển đến khách hàng cuối cùng khi giảm thời gian giao hàng và chi phí thấp hơn nhưng hàng hóa có chất lượng cao hơn.
Mặc dù các hệ thống MRP được vi tính hóa ban đầu yêu cầu cơ sở hạ tầng kỹ thuật rộng rãi, phần mềm MRP hiện đại chủ yếu chạy trên đám mây. Phần mềm không còn yêu cầu máy chủ tại chỗ hoặc bộ phận CNTT được chỉ định để duy trì cơ sở hạ tầng của nó. Những tiến bộ này đã làm cho việc sử dụng và triển khai loại phần mềm sản xuất này trở nên hợp lý hơn nhiều và sẵn có cho các nhà sản xuất thuộc mọi quy mô.
Việc các nhà cung cấp hệ thống MRP chuyển sang mô hình kinh doanh dựa trên đám mây và SaaS (Phần mềm dưới dạng dịch vụ) là khá gần đây. Chỉ khoảng 10 hoặc 15 năm trước, việc triển khai một hệ thống MRP sẽ tiêu tốn hàng trăm nghìn hoặc thậm chí hàng triệu đô la. Ngày nay, nhiều nhà cung cấp phần mềm cung cấp hệ thống của họ dưới dạng dịch vụ dựa trên web với phí đăng ký hàng tháng thấp. Một số hệ thống MRP thậm chí còn đi xa hơn và có thể truy cập thông qua thiết bị di động, giúp đơn giản hóa việc báo cáo tại cửa hàng và cũng cung cấp cho người quản lý cái nhìn sâu sắc về hoạt động của công ty từ mọi nơi.
MRP I – Lập kế hoạch yêu cầu vật liệu
Joseph Orlicky đã phát triển khái niệm này vào năm 1964 và công ty đầu tiên sử dụng nó là Black & Decker. Đây chỉ là thời điểm máy tính bắt đầu thống trị ngành công nghiệp.
So với các hệ thống MRP ngày nay, do những hạn chế về tính toán, MRP I là một phần mềm quản lý hàng tồn kho và lập kế hoạch sản xuất đơn giản hơn nhiều. Nó không được tích hợp nhiều để thu thập dữ liệu trực tiếp từ các bộ phận khác nhau của công ty.
Nó được thiết kế để trả lời một vài câu hỏi trọng tâm: Nên mua cái gì? Bao nhiêu? Khi nào?
Các dữ liệu đầu vào chính là:
- Các mặt hàng được sản xuất, hóa đơn nguyên vật liệu và chi tiết sản xuất (tức là định tuyến)
- Các mặt hàng vật liệu và thời gian giao hàng của họ.
- Nhu cầu bán hàng, dự báo doanh số bán hàng hoặc lịch trình sản xuất tổng thể
Các đầu ra dữ liệu chính là:
- Khuyến nghị về những gì nên được mua.
- Một lịch trình sản xuất cơ bản khi các hoạt động sản xuất khác nhau sẽ bắt đầu, bất kể công suất máy thực tế (giả sử công suất vô hạn)
Lợi ích chính là nhờ có máy tính, lịch trình sản xuất rõ ràng và các yêu cầu mua hàng xuất hiện tương đối dễ dàng. Ngoài ra, điều này sẽ mất nhiều giờ hàng ngày đối với một nhóm các nhà lập kế hoạch cho các sản phẩm phức tạp (hoặc chỉ nhiều bộ phận và sản phẩm!).
Nhược điểm lớn nhất là hệ thống MRP I không được tích hợp nhiều và để có kết quả tốt, dữ liệu cần được cập nhật liên tục. Ngoài ra, nó không cung cấp lịch trình sản xuất chính xác như vậy dựa trên công suất của từng máy, cũng như không quản lý tài chính sản xuất quan trọng như giá thành sản phẩm.

MRP II – Lập kế hoạch nguồn lực sản xuất
Lập kế hoạch nguồn lực sản xuất xuất hiện vào những năm 1980 khi các hệ thống MRP I được cải tiến và tích hợp với các ứng dụng kinh doanh khác. Do đó, hệ thống Lập kế hoạch Nguồn lực Sản xuất là một hệ thống tích hợp, trong đó nhiều hoạt động khác nhau trong một công ty sản xuất được tập hợp lại thành một hệ thống MRP thống nhất. Nó không còn chỉ là một ứng dụng cho một mục đích.
Hai trong số những cải tiến lớn nhất của MRP II là
- Khả năng tạo ra một lịch trình sản xuất có độ chính xác cao bằng cách xem xét năng lực sản xuất.
- Thông tin phản hồi trực tiếp từ khu vực cửa hàng, báo cáo và các chức năng khác, như quản lý hàng tồn kho, bán hàng, mua hàng, v.v.
Tất cả các bộ phận khác nhau trong công ty giao diện cùng một phần mềm trong thời gian thực – nhân viên bán hàng, người mua, nhân viên kho, người lập kế hoạch sản xuất, công nhân sản xuất, kỹ sư… tất cả họ đều có một nền tảng chung để thực hiện một số công việc của mình.
Vì mọi người đang sử dụng cùng một hệ thống vào cùng một thời điểm nên so với MRP I, dữ liệu trong hệ thống MRP II có chất lượng tốt hơn nhiều. Dữ liệu đơn giản là không cần phải chuyển từ hệ thống này sang hệ thống khác – trong khi là phần mềm mua bán, nó cũng là phần mềm quản lý hàng tồn kho, phần mềm sản xuất, hệ thống lập kế hoạch sản xuất, v.v.
Điều này có ý nghĩa gì đối với việc lập kế hoạch sản xuất?
- Bên cạnh việc cho bạn biết những gì nên mua, hệ thống MRP II có thể tự lập kế hoạch năng suất của tất cả các trạm làm việc, cung cấp một lịch trình sản xuất chi tiết. Trả lời câu hỏi “ Khi nào có hàng?”
- Vì việc mua nguyên vật liệu được thực hiện trong cùng một hệ thống, nên nó trả lời câu hỏi, “ Chi phí nguyên vật liệu là bao nhiêu?”
- Vì đây cũng là một hệ thống điều hành sản xuất nơi công nhân lập kế hoạch sản xuất và báo cáo, nên nó cũng trả lời các câu hỏi, “ Tình hình hiện tại ở xưởng là gì?”
- Và quan trọng, cũng dựa trên thông tin báo cáo, “ Chi phí sản xuất là bao nhiêu?”
- Vì việc bán hàng cũng được quản lý từ cùng một hệ thống nên nó tạo điều kiện thuận lợi rất nhiều cho việc lập kế hoạch giao hàng và giao hàng đúng hạn. Thêm vào đó, nó trả lời các câu hỏi quan trọng, “ Làm thế nào để định giá báo giá?” “Khi nào tôi có thể giao hàng?” và “ Công ty sẽ lãi bao nhiêu?”
- Và nhiều hơn nữa, tùy thuộc vào cách thức cụ thể mà hệ thống MRP đã được xây dựng.
Vì nhiều chức năng có thể được chuyển sang hệ thống MRP nên nó hỗ trợ rất nhiều cho việc lập kế hoạch sản xuất và thực hiện sản xuất. Việc quản lý tài chính dễ dàng hơn, có thông tin cập nhật về số dư hàng tồn kho, chi phí sản phẩm chính xác và báo cáo.
Một hệ thống MRP hiện đại là một hệ thống Hoạch định nguồn lực doanh nghiệp – một hệ thống MRP ERP – chứ không chỉ là một phân hệ như MRP đã từng ở giai đoạn sơ khai.
Các bước và quy trình của hệ thống MRP
Xác định các yêu cầu để đáp ứng nhu cầu.
Bước đầu tiên của quy trình MRP là xác định nhu cầu của khách hàng và các yêu cầu cần thiết để đáp ứng nhu cầu đó, bắt đầu bằng việc nhập đơn đặt hàng của khách hàng và dự báo doanh số bán hàng.
Sử dụng danh sách nguyên vật liệu cần thiết cho sản xuất, MRP sau đó phân tách nhu cầu thành các thành phần riêng lẻ và nguyên liệu thô cần thiết để hoàn thành công trình đồng thời tính đến mọi cụm lắp ráp phụ cần thiết.
Kiểm tra hàng tồn kho và phân bổ nguồn lực.
Bằng cách sử dụng MRP để kiểm tra nhu cầu đối với hàng tồn kho và phân bổ nguồn lực phù hợp, bạn có thể xem cả những mặt hàng bạn có trong kho và vị trí của chúng—điều này đặc biệt quan trọng nếu bạn có hàng tồn kho ở một số địa điểm. Điều này cũng cho phép bạn xem trạng thái của các mặt hàng, giúp hiển thị các mặt hàng đã được phân bổ cho một công trình khác, cũng như các mặt hàng chưa có trong kho thực tế đang được vận chuyển hoặc đang được đặt hàng. MRP sau đó di chuyển hàng tồn kho vào các vị trí thích hợp và nhắc các đề xuất sắp xếp lại.
Lập kế hoạch sản xuất.
Sử dụng lịch trình sản xuất tổng thể, hệ thống xác định lượng thời gian và lao động cần thiết để hoàn thành từng bước của mỗi bản dựng và thời điểm chúng cần diễn ra để quá trình sản xuất có thể diễn ra không bị chậm trễ.
Lịch trình sản xuất cũng xác định những máy móc và máy trạm nào cần thiết cho mỗi bước và tạo ra các đơn đặt hàng sản xuất, đơn đặt hàng và đơn đặt hàng chuyển giao thích hợp. Nếu quá trình xây dựng yêu cầu lắp ráp phụ, hệ thống sẽ tính đến lượng thời gian mà mỗi cụm lắp ráp cần và lên lịch cho chúng.
Xác định các vấn đề và đưa ra khuyến nghị.
Cuối cùng, vì MRP liên kết nguyên liệu thô với đơn đặt hàng sản xuất và đơn đặt hàng của khách hàng, nó có thể tự động cảnh báo nhóm của bạn khi các mặt hàng bị trì hoãn và đưa ra đề xuất cho các đơn hàng hiện có: tự động chuyển sản xuất vào hoặc ra, thực hiện phân tích tình huống giả định và tạo kế hoạch ngoại lệ để hoàn thành các bản dựng cần thiết.
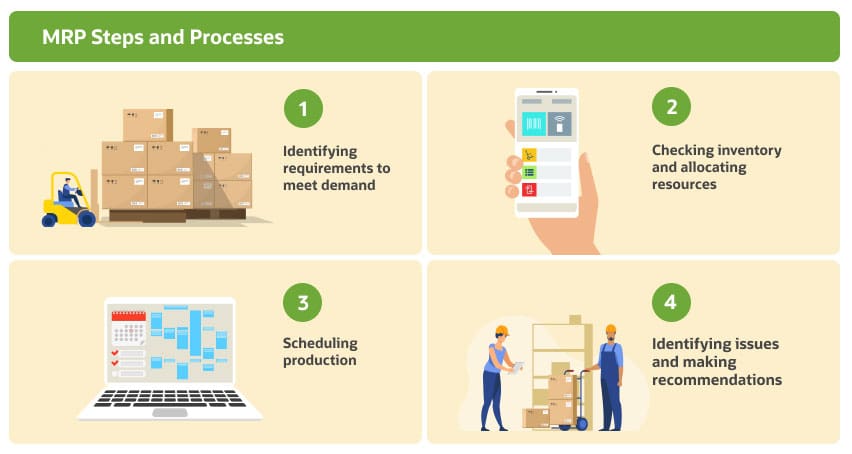
Các bước MRP bao gồm xác định các yêu cầu, kiểm tra hàng tồn kho, lập kế hoạch sản xuất và xác định các vấn đề. Nguồn : Netsuite.
Thông tin Đầu vào MRP
Từ góc độ kinh doanh, hai chức năng thiết yếu nhất mà hệ thống MRP thực hiện xuất sắc là:
1) Lập kế hoạch năng lực: Khi nào tôi có thể giao hàng?
2) Tính toán chi phí: Chi phí bao nhiêu?
Đối với hầu hết các công ty sản xuất, thông tin này tiến gần hơn 80% đến vạch đích. Vì vậy, hai mục tiêu này thường là quan trọng nhất. Hệ thống MRP của bạn hoạt động tốt như thế nào tùy thuộc vào chất lượng dữ liệu bạn cung cấp. Để hệ thống MRP hoạt động hiệu quả, mỗi đầu vào phải chính xác và được cập nhật. Dưới đây là một số yếu tố đầu vào mà MRP phụ thuộc vào:
Yêu cầu
Bao gồm dự báo bán hàng và đơn đặt hàng của khách hàng. Khi làm việc với nhu cầu dự đoán, một hệ thống được tích hợp với hệ thống ERP toàn doanh nghiệp cho phép dự báo bằng cách sử dụng doanh số bán hàng lịch sử thay vì chỉ dự đoán doanh số bán hàng.
Hóa đơn nguyên vật liệu (BOM)
Giữ một phiên bản cập nhật duy nhất của hóa đơn nguyên vật liệu là điều cần thiết để lập kế hoạch và dự báo cung ứng chính xác. Một hệ thống được tích hợp vào hệ thống quản lý hàng tồn kho toàn doanh nghiệp sẽ tránh được các vấn đề về kiểm soát phiên bản và chống lại các hóa đơn lỗi thời, dẫn đến việc phải làm lại và tăng lãng phí.
Máy móc, công đoạn và Định tuyến sản xuất (Routing) :
Danh sách các hoạt động, máy móc thiết bị – các bước quan trọng theo trình tự mà sản phẩm cần phải thực hiện.
Hàng tồn kho
Điều cần thiết là phải có chế độ xem hàng tồn kho trong toàn tổ chức theo thời gian thực để hiểu những mặt hàng nào bạn có trong tay và mặt hàng nào đang trên đường vận chuyển hoặc đã phát hành đơn đặt hàng, hàng tồn kho đó ở đâu và trạng thái của hàng tồn kho là gì.
Kế hoạch sản xuât Tổng thể
Lịch trình sản xuất tổng thể xem xét tất cả các yêu cầu xây dựng và lập kế hoạch sử dụng máy móc, nhân công và máy trạm để tính đến tất cả các đơn đặt hàng công việc chưa hoàn thành.
Đầu ra MRP
Sử dụng các đầu vào được cung cấp, MRP tính toán những vật liệu nào cần thiết, số lượng cần thiết để hoàn thành quá trình xây dựng và khi nào chúng cần trong quá trình xây dựng.
Với thông tin này được xác định, các doanh nghiệp có thể thực hiện sản xuất đúng lúc (JIT) , lập kế hoạch sản xuất dựa trên tình trạng sẵn có của vật liệu. Điều này giảm thiểu mức tồn kho và chi phí vận chuyển, vì hàng tồn kho không được lưu trữ trong kho để sản xuất trong tương lai mà được chuyển đến khi cần thiết. Bằng cách lên lịch vật liệu đến và sản xuất bắt đầu ngay sau đó, doanh nghiệp có thể di chuyển vật liệu thông qua quy trình công việc mà không bị chậm trễ.
MRP đưa ra kế hoạch về thời điểm vật liệu sẽ đến, dựa trên thời điểm chúng cần thiết trong quy trình sản xuất và thời điểm lắp ráp phụ nên được lên lịch. Sử dụng một kế hoạch sản xuất tổng thể và tính đến thời gian xây dựng lắp ráp phụ giúp giảm thiểu vật liệu nằm trên kệ và tắc nghẽn trong quá trình xây dựng.
Sự khác biệt giữa hệ thống MRP và ERP là gì?
Lập kế hoạch nguồn lực doanh nghiệp hoặc ERP là phần mềm được sử dụng để tích hợp tất cả các quy trình kinh doanh vào một gói duy nhất. Cũng như MRP II, chìa khóa của ERP nằm ở cơ sở dữ liệu thống nhất và xử lý dữ liệu. Sự khác biệt với MRP II là ERP bao gồm toàn bộ tổ chức, thay vì chỉ các quy trình tập trung vào sản xuất. Điều này có nghĩa là tất cả thông tin quan trọng trong kinh doanh có thể lưu chuyển tự do, trong thời gian thực, giữa tất cả các bộ phận liên quan.
Có nhiều loại ERP được cung cấp, có sẵn dưới dạng hệ thống tại chỗ hoặc dựa trên đám mây. Quy mô của các hệ thống ERP bao gồm từ các gói dành cho doanh nghiệp vừa và nhỏ (SME) đến các ERP dành cho doanh nghiệp lớn. Mặc dù hầu hết các hệ thống ERP bao gồm ít nhất một số dạng khả năng quản lý đơn hàng và hàng tồn kho, nhưng chúng thường được tối ưu hóa để quản lý và thống nhất các tổ chức và tập đoàn lớn hơn. Tuy nhiên, trong những năm gần đây, ngày càng có nhiều ERP tập trung vào sản xuất xuất hiện trên thị trường.
ERP sản xuất về cơ bản là một hệ thống MRP II mạnh mẽ cũng bao gồm các mô-đun cần thiết để vận hành tất cả các khía cạnh khác của doanh nghiệp. Nếu bạn là nhà cung cấp dịch vụ nhưng cũng có hàng tồn kho nhỏ với nhu cầu quản lý chuỗi cung ứng đơn giản, hệ thống ERP thông thường hoặc hệ thống CRM trực tuyến sẽ thực hiện công việc. Mặt khác, nếu bạn là nhà sản xuất và cần quản lý dây chuyền sản xuất nhưng cũng muốn tăng cường kiểm soát đối với CRM, nguồn nhân lực và tài chính của mình thì ERP sản xuất là lựa chọn tốt nhất.
Nhiều giải pháp ERP hiện đại thậm chí còn đi xa hơn và bao gồm tích hợp sẵn với phần mềm tài chính như QuickBooks hoặc Xero hoặc phần mềm Thương mại điện tử và CRM như Shopify hoặc Salesforce . Nhìn chung, một ERP sản xuất dựa trên đám mây tốt sẽ tạo thành ưu đãi tốt nhất cho các nhà sản xuất thuộc mọi loại hình và quy mô.
Nguồn MRPEasy & Netsuite.