Sử dụng phần mềm và phần cứng đã được kiểm nghiệm, Siemens đã phát triển một giải pháp phân tán nơi làm việc độc đáo giúp các nhà sản xuất mô phỏng và quản lý rủi ro phơi nhiễm của nhân viên trong khi cho phép năng suất trong toàn bộ cơ sở của họ.
Đại dịch đã làm cho khá rõ ràng rằng sẽ sớm có một bình thường mới cho các nhà sản xuất. Do đó, các nhà sản xuất đang đối mặt với một loạt các thách thức khi họ bắt đầu quá trình khởi động lại các hoạt động thường xuyên. Trong khi tìm ra và cuối cùng điều hướng thực tế hoạt động mới này, các nhà sản xuất phải xem xét các khía cạnh bổ sung về an toàn của nhân viên, bao gồm việc thiết lập môi trường sản xuất và quy trình làm việc giải quyết các yêu cầu xa cách vật lý.
Kết hợp phần cứng và phần mềm đã được kiểm nghiệm, Siemens đã tạo ra một giải pháp mới cho phép các công ty mô hình hóa nhanh chóng và hiệu quả cách các nhân viên tương tác với nhau, dây chuyền sản xuất và thiết kế nhà máy. Giải pháp mới cũng cho phép các tổ chức xây dựng một bộ đôi kỹ thuật số đầu cuối, để mô phỏng sự an toàn của công nhân, lặp lại và tối ưu hóa bố trí không gian làm việc và xác nhận các biện pháp an toàn và hiệu quả để giúp các dây chuyền sản xuất trong tương lai.
Với Hệ thống định vị thời gian thực SIMATIC (RTLS) của Siemens, các công ty có thể liên tục đo khoảng cách giữa các công nhân, cung cấp phản hồi trực quan theo thời gian thực cho nhân viên về khoảng cách giữa họ với người khác và tạo ra nhật ký của tất cả các chuyển động và tương tác theo thời gian. Theo cách này, SIMATIC RTLS của Siemens liên tục tạo điều kiện cho khoảng cách an toàn trong khi vẫn cung cấp nhiều lợi ích bổ sung khác.
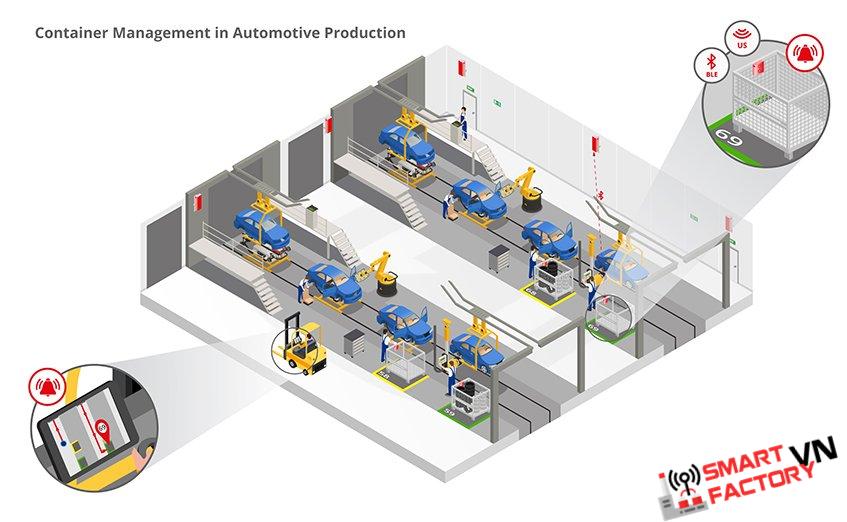
“Chúng tôi đã luôn nói về mô phỏng. Chúng tôi đã nói về việc thực hiện hầu như trước khi bạn thực hiện nó và tôi nghĩ điều này rất quan trọng. Bây giờ hơn bao giờ hết, nơi bạn luôn không thể ở đó, nhưng bạn có thể làm rất nhiều POC và các hệ thống nhúng kiểm tra hầu hết trong các công cụ mô phỏng. Và trong khi những thứ này vốn không được thiết kế cho cuộc khủng hoảng COVID-19, thì ngày nay chúng rất phù hợp “, nói. Raj Batra, chủ tịch của Siemens Digital Industries của Hoa Kỳ.
Kết hợp SIMATIC RTLS của Siemens với một bộ đôi kỹ thuật số của môi trường sản xuất thực tế cho phép các công ty mô hình hóa và mô phỏng cách các nhân viên tương tác với thiết bị với nhau, cho phép họ lặp lại và tối ưu hóa an toàn và năng suất trong thời gian ngắn và xác nhận thiết kế lại toàn bộ hoạt động trước khi thay đổi vật lý tốn kém hơn được thực hiện.
Bằng cách thu thập dữ liệu thời gian thực, các nhà sản xuất có cơ hội thúc đẩy ý tưởng lặp lại liên tục các thông tin được thu thập trong giai đoạn xác nhận, cho phép họ phân tích. giải quyết và kiểm tra lại các bản cập nhật trên sàn sản xuất. Vì vậy, cho dù đó là xem xét các tương tác lưu lượng, lưu lượng vật liệu hoặc các thông số sản xuất khác, có thể điều khiển các bản cập nhật cho dòng và mô phỏng các hoạt động thực tế. Chủ đề kỹ thuật số này tạo ra một cơ hội để xác định các vấn đề khi chúng xuất hiện, thúc đẩy các bản cập nhật và việc thực hiện có thể xảy ra tương đối nhanh chóng.
Chúng tôi đang giúp khách hàng của mình tạo ra một môi trường làm việc an toàn, điều này cực kỳ quan trọng khi họ tìm cách sản xuất hiệu quả và đáng tin cậy trong những tình huống chưa từng có, ông Tony Hemmelgarn, chủ tịch và CEO của Công ty Siemens Digital Industries cho biết.
Sự kết hợp giữa quản lý khoảng cách thời gian thực và mô phỏng kỹ thuật số sẽ giúp các công ty duy trì môi trường làm việc an toàn ngày nay và đưa ra quyết định có giáo dục về tối ưu hóa liên tục và lâu dài.
Để thực hiện giải pháp này, các bộ phát đáp SIMATIC RTLS của Siemens (với độ chính xác khoảng một bước chân) được gắn trong các huy hiệu được đeo như một thiết bị bảo vệ cá nhân của tất cả nhân viên.Máy thu RTLS được đặt trong suốt quá trình hoạt động sau đó có thể liên tục theo dõi và ghi lại chuyển động của lực lượng lao động. Khi hai nhân viên rơi vào tình huống rủi ro (ví dụ, cách nhau dưới sáu feet), huy hiệu của họ sẽ hiển thị cảnh báo, cảnh báo họ về tình huống. Dữ liệu được thu thập theo thời gian có thể được phân tích để xác định các điểm nóng trong nhà máy, nơi các tình huống rủi ro xảy ra thường xuyên. Những tình huống như vậy trở nên dễ dàng thực hiện thông qua bộ đôi kỹ thuật số, được cung cấp bởi phần mềm mô phỏng nhà máy Tecnomatix của Siemens. Sử dụng dữ liệu thu thập được, bố trí sản xuất mới hoặc quy trình công việc có thể được mô phỏng cho đến khi xác định được kết quả mong muốn,
Ngoài ra, các nhà sản xuất có thể thêm khả năng truy nguyên nguồn gốc vào giải pháp thông qua các giải pháp tại cơ sở của Siemens hoặc một ứng dụng như Ứng dụng truy xuất nguồn gốc đáng tin cậy của Siemens trên MindSphere, 1 hệ điều hành IoT mở, dựa trên đám mây của Siemens, cho phép phân tích liên hệ nhanh chóng, toàn diện trong trường hợp không may lây nhiểm tại nơi làm việc thực tế. Tất cả các chuyển động và liên hệ với nhân viên bị ảnh hưởng có thể được hình dung, cho phép thông báo nhanh chóng về những người tiếp xúc gần gũi và làm sạch sâu (chọn toàn bộ site ) trong môi trường vật lý tiếp xúc.
Và khi bộ quy tắc khủng hoảng lắng xuống, những công nghệ và công cụ này có thể được triển khai lại trong cơ sở hạ tầng sản xuất chung để phòng ngừa đợt 2 của dịch. Đây là một công nghệ đã được điều chỉnh cho COVID-19 để tạo khoảng cách xã hội. Công nghệ này thường xử lý theo dõi tài sản, làm việc theo tiến độ, hậu cần và kiểm soát sản xuất ứng dụng, làm cho nó trở thành một nhà sản xuất công nghệ có thể sử dụng để tối ưu hóa quy trình của họ.