Manufacturing is the process of transforming raw materials into finished products through various physical, chemical, or mechanical means. Here is all you need to know as a newcomer to the industry.
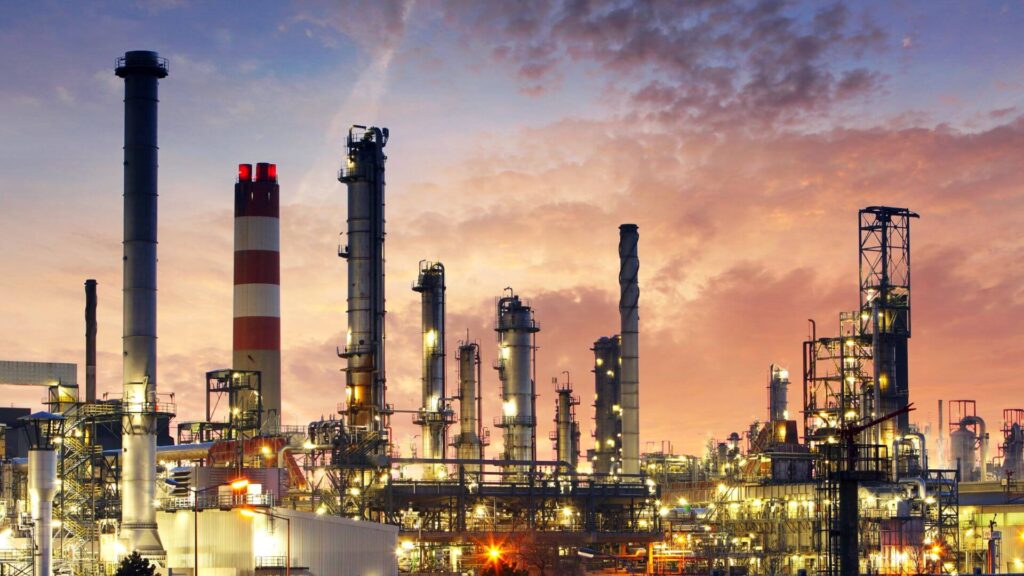
What is manufacturing?
Manufacturing is the process of transforming raw materials into finished products through various physical, chemical, or mechanical means. This transformation process is fundamental to the growth and sustainability of the global economy, influencing every aspect of our daily lives, from the food we eat to the clothes we wear to the machines we use to work and communicate.
The manufacturing sector encompasses a vast array of industries, from automotive and aerospace to electronics and consumer goods.
Key manufacturing industries
The manufacturing sector is diverse, encompassing a wide range of industries that produce a variety of goods. Here’s a list of key manufacturing industries:
- Automotive industry. Involves the production of cars, trucks, buses, and other vehicles, including parts manufacturing like engines and bodywork. Notable examples include Ford, Toyota, Volkswagen.
- Aerospace and defense. Focuses on the manufacturing of aircraft, spacecraft, satellites, military vehicles, and associated components. Notable examples include Airbus, Lockheed Martin, Raytheon.
- Chemicals. Produces basic chemicals, specialty chemicals, agricultural chemicals, pharmaceuticals, and petrochemicals. Notable examples include Dow Chemicals, DuPont, Bayer.
- Electronics. Encompasses the production of consumer electronics, semiconductors, electronic components, and industrial electronics. Notable examples include Apple, Samsung, NVIDIA.
- Food and beverage. Involves the transformation of raw food ingredients into packaged food products. Notable examples include The Coca-Cola Company, Unilever, Mondelez.
- Industrial machinery. Includes the manufacturing of machines for other industries, like agriculture, construction, and mining machinery. Notable examples include Caterpillar, Siemens, Deere.
- Textiles and apparel. Covers the production of fibers, yarns, fabrics, and clothing, as well as accessories. Notable examples include Adidas, Inditex, H&M.
- Pharmaceuticals. A subsector of the chemical industry that focuses on the production of medicinal drugs. Notable examples include Pfizer, Roche, Merck.
- Plastics and rubber. Involves the production of plastic and rubber materials, including the manufacturing of products made from these materials. Notable examples include Goodyear, Covestro, BASF.
- Paper and printing. Includes the manufacturing of paper goods, such as books, newspapers, packaging materials, and stationery. Notable examples include Kimberly-Clark, Georgia-Pacific, International Paper Company.
- Metals manufacturing. Encompasses the production of metal materials and products, including steel, aluminum, and copper goods. Notable examples include Nippon Steel Corporation, ArcelorMittal, ThyssenKrupp.
- Furniture. Involves the production of household, office, and institutional furniture, as well as mattresses and blinds. Notable examples include IKEA, Herman Miller, Steelcase.
- Consumer goods. Broad category that includes manufacturing of household appliances, toys, sports equipment, and other products intended for personal use. Notable examples include Procter & Gamble, Colgate-Palmolive, Unilever.
- Building materials and construction. Covers the production of construction materials, such as cement, bricks, glass, and fixtures. Notable examples include Saint-Gobain, CEMEX, LafargeHolcim.
- Energy. Although not traditionally categorized under manufacturing, it includes the production of energy equipment, like solar panels and wind turbines, contributing significantly to the manufacturing landscape. Notable examples include General Electric, First Solar, Siemens.
- Medical devices. Specializes in the production of equipment used for medical treatment and diagnosis, such as surgical instruments and diagnostic machines. Notable examples include Medtronic, Abbott Laboratories, Siemens Healthineers.
These industries are integral to the global manufacturing landscape, each playing a vital role in economic development, innovation, and the provision of essential goods and services.
Why is manufacturing important?
First of all, manufacturing creates the products we all use in our daily life. This enables economic diversification as it frees up labor for other industries. As such, manufacturing plays a major role in the global economy, driving innovation, economic growth, and job creation.
Manufacturing is a key driver of competitiveness, as it fosters innovation and productivity gains that contribute to a nation’s economic strength. It adds value to raw materials, creating finished products that meet consumer needs and drive consumption.
Moreover, manufacturing generates significant employment opportunities, providing jobs for millions of people worldwide. Workforce development is essential in this sector, as skilled workers are needed to operate machinery, manage production processes, and drive innovation in product design and development.
Manufacturing also plays a crucial role in supply chain management, as it involves the coordination of various activities from sourcing raw materials to delivering finished products to consumers. This interconnectedness ensures the efficient flow of goods and contributes to overall economic stability.
Furthermore, the manufacturing sector has a substantial impact on gross domestic product (GDP), with countries like China, the United States, and Germany famously relying heavily on manufacturing output to drive economic growth.
In summary, manufacturing is essential for driving economic prosperity, creating jobs, fostering innovation, and meeting consumer demand for a wide range of goods. Its importance extends beyond individual industries, shaping the overall economic landscape and contributing to global development and well-being.
History of modern manufacturing
The roots of modern manufacturing can be traced back to the Industrial Revolution of the late 18th and early 19th centuries, a period marked by the mechanization of production processes.
Before that, goods were primarily crafted by hand using traditional methods and tools. Production was labor-intensive, with skilled artisans and craftsmen working in small-scale workshops or at home to create goods one at a time.
The era of the Industrial Revolution saw the birth of mechanized innovations like the steam engine and spinning jenny, propelling the shift from agrarian economies to industrial powerhouses. This revolution spurred rapid growth in the manufacturing sector, particularly in textiles, iron, and coal industries, setting the stage for first the UK’s and then America’s industrial dominance.
The 20th century ushered in groundbreaking advancements, epitomized by Henry Ford’s introduction of the assembly line which revolutionized mass production and made automobiles and consumer goods more accessible than ever before. World War II had a profound impact on manufacturing technology, driving rapid advancements to meet the demands of wartime production. The war spurred innovations such as the development of new materials like synthetic rubber and plastics, and the widespread adoption of automation and assembly line methods. Additionally, the war accelerated the development of technologies such as the computer, radar, jet engines, and nuclear power, which had significant implications for manufacturing and industry in the post-war period.
Japan emerged as a global leader in manufacturing excellence, championing lean manufacturing principles that grew out of companies like Toyota. This new manufacturing philosophy emphasized waste reduction and value maximization and became one of the leading paradigms of manufacturing management. Meanwhile, the latter half of the century saw the advent of robotics, additive manufacturing, or 3D printing, enabling rapid prototyping and customization of products.
The 21st century has seen manufacturing evolve with smart technologies powered by manufacturing analytics and artificial intelligence, driving unprecedented levels of efficiency and agility. Globalization has also transformed manufacturing, with supply chains spanning continents and reshaping the competitive landscape. In addition, China has replaced Japan as the manufacturing powerhouse of the Eastern Hemisphere, even overcoming the US as the largest global economy.
The state of manufacturing in 2024
The current state of manufacturing presents diverse trends across key regions, reflecting global dynamics and technological advancements.
China
China continues to dominate global manufacturing, with a focus on advanced manufacturing techniques and innovation-driven growth. Despite facing challenges such as rising labor costs and trade tensions, China remains a powerhouse in manufacturing jobs and production. The country is investing heavily in smart manufacturing technologies and Industry 4.0 initiatives to maintain its competitive edge and drive value-added manufacturing.
Often referred to as “the world’s factory”, China is known for its massive and diverse manufacturing output that includes everything from electronics, textiles, and machinery to plastics, metal, and automotive components.
USA
In the USA, there’s a resurgence in manufacturing, fueled by a combination of reshoring initiatives and the evolution of advanced manufacturing. This has led to the creation of new products and the revitalization of US manufacturing businesses. Investments in smart manufacturing and workforce development initiatives by American manufacturing institutes and other organizations are driving innovation and improving the manufacturing value chain.
The United States is a leading producer of aerospace and defense equipment, automotive vehicles and parts, pharmaceuticals, machinery, and electronics.
UK
The United Kingdom (UK) has a long history of manufacturing excellence, although its manufacturing sector has undergone significant transformations over the years. While the UK was once a global leader in industries such as textiles, steel, and shipbuilding, its manufacturing landscape has evolved to focus more on high-tech and specialized manufacturing sectors.
Today, the UK’s main manufacturing exports include aerospace and automotive products, industrial machinery, pharmaceuticals, and food and beverages.
Europe
Europe’s manufacturing landscape is characterized by innovation and sustainability, with countries like Germany leading in advanced manufacturing practices. European manufacturers are embracing new technologies to improve productivity and efficiency while reducing environmental impact. Initiatives focused on value-added manufacturing and workforce development are improving Europe’s competitiveness in the global market.
Europe’s manufacturing output is diverse and includes automobiles, machinery, chemicals, aerospace products, pharmaceuticals, and luxury goods such as fashion and design items. Countries like Germany, Italy, and France are particularly renowned for their manufacturing expertise in sectors like automotive and machinery.
World
Globally, manufacturing trends are shaped by technological advancements and shifts in consumer preferences. There is a growing emphasis on smart manufacturing practices and the adoption of Industry 4.0 technologies to drive efficiency and agility in production processes. Manufacturers worldwide are exploring new opportunities for value-added manufacturing and investing in workforce development to remain competitive in the global marketplace.
Global supply chain disruptions are significantly impacting manufacturing by causing delays in the delivery of raw materials, components, and finished goods, leading to production slowdowns and increased costs. These disruptions, exacerbated by factors such as transportation bottlenecks, labor shortages, and geopolitical tensions, are forcing manufacturers to adapt their sourcing strategies, diversify supply chains, and implement resilience measures to mitigate risks and ensure continuity of operations.
Overall, the state of manufacturing today is characterized by innovation, digitization, and a focus on sustainability. By embracing modern techniques and investing in workforce development, countries and regions can strengthen their manufacturing sectors and drive economic growth in the 21st century.
Emerging trends in manufacturing
Emerging trends in manufacturing are reshaping the industry landscape, driving innovation, efficiency, and sustainability. Here are some of the emerging trends of today:
- Additive manufacturing (3D printing). This trend involves the layer-by-layer construction of objects using digital models. Additive manufacturing offers increased design flexibility, reduced waste, and the ability to produce complex geometries, making it ideal for rapid prototyping and customized production.
- Internet of Things (IoT) integration. IoT integration refers to the connection of physical devices and systems within the manufacturing environment to collect and exchange data. By leveraging IoT technologies, manufacturers can achieve real-time monitoring, predictive maintenance, and process optimization, leading to increased efficiency and reduced downtime.
- Artificial intelligence (AI) and machine learning. AI and machine learning technologies are revolutionizing manufacturing by enabling predictive analytics, autonomous operations, and adaptive control systems. These technologies empower manufacturers to optimize production processes, improve quality, and make data-driven decisions for improved productivity and competitiveness.
- Blockchain technology. Blockchain technology offers secure, transparent, and tamper-resistant data management solutions for supply chain traceability, quality assurance, and transactional integrity. By leveraging blockchain, manufacturers can increase trust, visibility, and efficiency across their supply chains while mitigating risks associated with counterfeit products and unauthorized modifications.
- Sustainable manufacturing practices. Sustainable manufacturing practices involve minimizing environmental impact, conserving resources, and promoting social responsibility throughout the production process. From renewable energy adoption to waste reduction initiatives and eco-friendly materials usage, manufacturers are increasingly prioritizing sustainability to meet regulatory requirements, consumer demands, and corporate sustainability goals.
8 basic steps of manufacturing a product
The manufacturing process involves several key steps, each essential for transforming raw materials into finished products efficiently and effectively.
- Product design. The first step is to conceptualize and design the product. This stage involves researching market needs, designing prototypes, and refining product specifications to meet consumer demands and manufacturing capabilities.
- Raw material acquisition. Once the product design is finalized, raw materials are sourced from suppliers. This step involves assessing quality, negotiating contracts, and ensuring timely delivery to meet production schedules.
- Production planning. Manufacturing companies develop production plans to outline the sequence of operations, allocate resources, and optimize production efficiency. Forecasting demand and scheduling production runs are critical aspects of this step.
- Production. Actual production begins with the transformation of raw materials into finished products. This may involve various processes ranging from mixing and baking to welding, machining, 3D printing, etc. depending on the product, its design, and manufacturing requirements.
- Assembly and integration. For products with multiple components, assembly lines are utilized to streamline the assembly process. Components are assembled, tested, and integrated into the final product according to predetermined specifications.
- Quality control. Throughout the manufacturing process, quality control measures are implemented to ensure that products meet predefined standards and specifications. This involves inspecting raw materials, monitoring production processes, and testing finished products for defects.
- Packaging and shipping. Once products pass quality control checks, they are packaged according to customer requirements and prepared for shipment. This involves labeling, packing, and arranging transportation to deliver finished products to customers or distribution centers.
- Post-production support. Manufacturing companies may provide post-production support services such as warranty repairs, technical assistance, and customer service to ensure customer satisfaction and maintain product quality.
By following these basic steps, manufacturing companies can efficiently produce high-quality products that meet customer needs and drive business success.
Manufacturing processes explained
A manufacturing process involves the utilization of machinery, equipment, or natural reactions to transform raw materials or components into finished goods consistently and repeatedly. Irrespective of a company’s size or the complexity of its product range, every factory has devised and implemented a manufacturing process tailored to its product and production type.
The choice of process is often dictated by the nature of the product, with some requiring a straightforward approach while others necessitate intricate midstream procedures such as mixing or blending. However, it’s not uncommon to observe variations in manufacturing processes across different companies or even within the same manufacturing entity.
Manufacturing processes can be categorized in different ways. Let’s take a closer look at these categories.
Manufacturing processes by the nature of the process
- Chemical manufacturing processes. Chemical manufacturing processes involve the transformation of raw materials through chemical reactions to produce desired products. These processes often require precise control of temperature, pressure, and chemical composition to achieve the desired outcomes. Examples of chemical manufacturing processes include fermentation, polymerization, distillation, and chemical synthesis. These processes are commonly used in industries such as pharmaceuticals, petrochemicals, and specialty chemicals.
- Physical manufacturing processes. Physical manufacturing processes rely on physical forces and energy to alter the shape, form, or properties of materials. These processes do not involve chemical changes in the materials and primarily focus on mechanical or thermal manipulation. Examples of physical manufacturing processes include machining, welding, drilling, forging, casting, extrusion, 3D-printing, lithography, and heat treatment. These processes are prevalent in industries such as metalworking, automotive, aerospace, and construction.
- Biomanufacturing processes. Biomanufacturing utilizes biological systems or organisms to produce valuable products such as pharmaceuticals, enzymes, and biofuels. Processes such as fermentation, cell culture, and genetic engineering are used in biomanufacturing facilities.
- Assembly. Assembly is a critical manufacturing process involving the integration of individual components or parts to create a finished product. It often occurs after various manufacturing processes like machining, casting, or molding. Assembly lines or workstations streamline this process, ensuring efficiency and consistency. Depending on the complexity of the product, assembly can range from manual to automated.
Manufacturing processes by scale of production
- Job shop manufacturing. In job shop production processes, products are typically manufactured individually or in small series, often ranging from one to two dozen per month. This approach allows for a wide range of products to be produced, using universal equipment, devices, cutting, and measuring tools for general purposes. Workplaces are grouped based on technologically homogeneous operations, with no specific operations assigned to individual employees. Employees are highly qualified to handle the diverse nature of work performed. However, detailed development of the technological process for manufacturing the product is limited. Planning, regulation, and accounting focus on the entire product or its large units (subassemblies), resulting in relatively low costs for preparing production of new products. This type of one-off manufacturing process is common in pilot plants that produce complex products and special-purpose systems.
- Batch (or serial) manufacturing. Serial production processes involve the periodic production of products in batches, with small batches typically ranging from several hundred to large-scale batches of 2-5 thousand pieces per month. While there is a limited range of products manufactured, universal and specialized equipment, attachments, finishing, and measuring tools are used. Workplaces are grouped based on technological and organizational principles, with a limited number of different operations assigned to each workplace. Employees have a moderate level of qualification, and there is detailed development of technological processes. Planning, rationing, and accounting focus on the units and details of the product, resulting in relatively high costs for preparing production of new products compared to single-type production. This type of manufacturing process is common in process manufacturing as well as in factories producing sophisticated products and special-purpose systems that undergo frequent design changes.
- Mass production. Mass production processes involve the manufacture of products in large quantities, using specialized and special equipment, devices, and tools. Workstations are arranged according to the flow of the technological process, with each workstation specializing in performing one operation. The technological process is developed in detail, with planning, rationing, and accounting focusing on the details and operations. Workers may have lower qualifications, and preparation for producing new products requires the highest costs compared to other types of production. This type of manufacturing process is predominantly used in producing consumer goods.
Manufacturing processes by the nature of the product
- Discrete manufacturing. Discrete manufacturing involves the production of distinct items or products that are easily identifiable as separate entities. These products are typically assembled from individual components or parts through assembly or fabrication processes. Examples of discrete manufacturing include the production of automobiles, consumer electronics, furniture, machinery, and toys. In discrete manufacturing, each unit produced is unique and can be customized to meet specific customer requirements. This type of manufacturing is often characterized by high variability, short production runs, and the use of assembly lines or workstations to assemble components into finished products.
- Process manufacturing. Process manufacturing, on the other hand, involves the production of goods that are produced through a series of continuous or sequential processes. Unlike discrete manufacturing, where products are assembled from individual components, process manufacturing involves mixing, blending, or transforming raw materials or ingredients to create the final product. Examples of process manufacturing industries include chemical processing, food and beverage production, pharmaceutical manufacturing, and oil refining. Process manufacturing is characterized by standardized recipes or formulations, continuous production flows, and the use of specialized equipment such as reactors, mixers, and distillation columns. Products manufactured through process manufacturing often undergo physical or chemical changes during production and are typically produced in large quantities.
What is lean manufacturing?
Lean manufacturing is a production methodology focused on maximizing efficiency and minimizing waste throughout the manufacturing process. Originating from the Toyota Production System (TPS) developed by Toyota in the 1950s, lean principles aim to optimize operations, increase productivity, and improve overall value for customers.
At its core, lean manufacturing revolves around the concept of eliminating the 8 wastes of lean manufacturing, known as “muda” in Japanese. This waste can manifest in various forms, including overproduction, excess inventory, defects, waiting times, unnecessary transportation, overprocessing, and underutilized talent. Lean principles emphasize the identification and elimination of these inefficiencies to streamline processes and deliver products or services with higher quality, lower costs, and shorter lead times.
Key principles of lean manufacturing include:
- Continuous improvement (kaizen). Encouraging a culture of continuous improvement where employees at all levels are empowered to identify and implement small, incremental changes to improve processes and eliminate waste.
- Just-in-time (JIT) production. Just-in-time manufacturing minimizes inventory levels by producing goods only in response to customer demand, thereby reducing carrying costs, storage space, and the risk of obsolescence.
- Pull production. Establishing a production system where work is pulled through the system based on customer demand, rather than pushing products through based on production schedules. See also push vs. pull systems.
- Value stream mapping. Analyzing and visualizing the flow of materials and information throughout the entire production process to identify areas of waste and opportunities for improvement.
- Standardized work. Establishing standardized procedures and work instructions to ensure consistency, quality, and efficiency in production processes.
- Respect for people. Recognizing the importance of engaging and empowering employees, fostering a culture of respect, collaboration, and continuous learning.
By adopting lean manufacturing principles, organizations can achieve significant improvements in productivity, quality, lead times, and customer satisfaction while reducing costs and increasing competitiveness in the global marketplace.
What is manufacturing software?
Manufacturing software refers to specialized software applications designed to streamline and optimize various aspects of manufacturing operations. These software solutions are tailored to meet the unique needs of manufacturing businesses, helping them manage production processes, inventory, resources, and supply chains more effectively.
Manufacturing software typically encompasses a wide range of functionalities, including production planning and scheduling, inventory management, shop floor control, quality management, procurement, and reporting. These functionalities are often integrated into a comprehensive manufacturing execution system (MES) or enterprise resource planning (ERP) software.
Key features of manufacturing software may include:
- Production planning and scheduling. Software tools that enable manufacturers to plan production activities, allocate resources, and create schedules to meet production targets efficiently.
- Inventory management. Solutions for managing inventory levels, tracking raw materials, components, and finished goods, optimizing stock levels, and reducing carrying costs.
- Shop floor control. Tools for monitoring and controlling manufacturing processes in real-time, tracking work orders, and managing workflow on the shop floor.
- Quality management. Systems for ensuring product quality and compliance with industry standards and regulations through quality control inspections, testing, and corrective actions.
- Procurement. Modules for managing supplier relationships, sourcing raw materials, components, and services, and optimizing procurement processes to reduce costs and lead times.
- Reporting and analytics. Reporting tools that provide insights into key performance indicators (KPIs), production metrics, and other operational data to support decision-making and continuous improvement efforts.
Manufacturing software plays a critical role in increasing efficiency, productivity, and competitiveness in the manufacturing sector. By automating and streamlining core processes, manufacturers can reduce waste, minimize errors, improve quality, and ultimately deliver better products to customers while maximizing profitability. Additionally, with the advent of Industry 4.0 technologies such as IoT, AI, and big data analytics, modern manufacturing software solutions are evolving to provide even more advanced capabilities for predictive maintenance, real-time monitoring, and adaptive manufacturing.
Key takeaways
- Manufacturing is the process of converting raw materials into finished products and plays a crucial role in the global economy across various industries.
- Key manufacturing industries range from automotive and aerospace to electronics, textiles, and pharmaceuticals, each contributing to economic development and innovation.
- Manufacturing drives economic growth, job creation, and competitiveness, emphasizing the importance of workforce development and innovation.
- The history of modern manufacturing traces back to the Industrial Revolution and has since evolved through technological advancements and globalization.
- The current state of manufacturing reflects diverse trends across regions, with China, the USA, Europe, and other regions investing in advanced manufacturing technologies and initiatives.
- Emerging trends in manufacturing include additive manufacturing, IoT integration, AI and machine learning, blockchain technology, and sustainable practices, shaping the industry’s future.
- Understanding manufacturing processes, lean manufacturing principles, and the role of manufacturing software is essential for optimizing operations, improving efficiency, and driving competitiveness in the 21st century.
Frequently asked questions
Emerging trends like additive manufacturing and IoT integration impact manufacturing industries by enabling rapid prototyping, customization, and real-time monitoring, leading to increased efficiency and product quality across sectors.
Blockchain technology increases supply chain transparency by providing secure, tamper-resistant data management solutions. They enable traceability throughout the manufacturing process, reducing the risk of counterfeit products and unauthorized modifications while ensuring integrity and compliance with regulations.
Common challenges in adopting manufacturing software include integration issues with existing systems, employee resistance to change, and the need for training and support to maximize the software’s potential and overcome implementation hurdles.
You may also like: Manufacturing Operations Management (MOM) Processes and Tips
Nguồn : https://www.mrpeasy.com/blog/manufacturing/.
Post By Automation Bot.