Ở Việt Nam, hầu như ai làm ngành sản xuất đều biết Lean Manufacturing (tạm dịch là Sản Xuất Tinh Gọn) là một nhóm phương pháp, hiện đang được áp dụng ngày càng rộng rãi trên khắp thế giới, nhằm loại bỏ lãng phí và những bất hợp lý trong quy trình sản xuất, để có chi phí thấp hơn và tính cạnh tranh cao hơn cho nhà sản xuất.
Tuy nhiên để triển khai Lean Manufacturing không phải là vấn đề dễ dàng tại Việt Nam trước đây do vấn đề về công nghệ, và sự quyết tâm của người làm sản xuất. Để làm rõ vấn đề vai trò của MES – MOM và số hóa sản xuất sẽ hỗ trợ doanh nghiệp như thế nào, SmartfactoryVN xin giới thiệu loạt bài để cho bạn đọc hình dung việc áp dụng số hóa và triển khai MES – MOM sẽ mang lại những lợi ích gì cho kế hoạch triển khai Lean Manufacturing, một trong những ứng dụng có thể thấy rõ nhất của hệ thống sản xuất số.
Trước khi nói rõ hơn về vấn đề đó, SmartIndustryVN xin nhắc lại một số kiến thức nền tảng và phương pháp luận của Lean Manufacturing.
Lean Manufacturing và lịch sử ra đời
Nhiều khái niệm về Lean Manufacturing bắt nguồn từ Hệ thống sản xuất Toyota (TPS) và đã được dần triển khai xuyên suốt các hoạt động của Toyota từ những năm 1950. Từ trước những năm 1980, Toyota ngày càng được biết đến nhiều hơn về tính hiệu quả trong việc triển khai hệ thống sản xuất Just In Time (JIT).ua72
Ngày nay, Toyota thường được xem là một trong những công ty sản xuất hiệu quả nhất trên thế giới và là công ty đã đưa ra chuẩn mực về điển hình áp dụng Lean Manufacturing. Cụm từ “Lean Manufacturing” hay “Lean Production” đã xuất hiện lần đầu tiên trong quyển “The Machine that Changed the World” (Cỗ máy làm thay đổi Thế giới , Daniel Jones & Daniel Roos) xuất bản năm 1990.
Lean Manufacturing đang được áp dụng ngày càng rộng rãi tại các công ty sản xuất hàng đầu trên toàn thế giới, dẫn đầu là các nhà sản xuất ôtô lớn và các nhà cung cấp thiết bị cho các công ty này. Lean Manufacturing đang trở thành đề tài ngày càng được quan tâm tại các công ty sản xuất ở các nước phát triển khi các công ty này đang tìm cách cạnh tranh hiệu quả hơn.
Lợi ích Lean Manufacturing
Lean Manufacturing có mục đích là nhận thức và loại bỏ các loại lãng phí (lãng phí: những công việc không mang lại giá trị gia tăng cho khách hàng), sử dụng vượt mức nguyên liệu đầu vào, phế phẩm và chi phí liên quan đến tái chế phế phẩm, các tính năng sản phẩm không được khách hàng yêu cầu.
- Giảm chu kỳ sản xuất: giảm thời gian chờ đợi giữa các công đoạn, thời gian thời gian chuẩn bị, thời gian từ kho đến kho, thời gian làm sản phẩm
- Giảm tồn kho: ở mức tối thiểu và an toàn trong sản xuất, vốn lưu động ít hơn, giảm mặt bằng sản xuất, lưu kho thành phẩm và bán thành phẩm.
- Tăng năng suất lao động: không thực hiện các thao tác không cần thiết, giảm thời gian chờ đợi giữa các khâu, dòng chảy sản phẩm liên tục.
- Sử dụng thiết bị và mặt bằng hiệu quả: bố trí theo sơ đồ truyền Lean, sắp xếp công nhân theo hình dưới. Sẽ tận dụng được số công nhân và mặt bằng sản xuất.
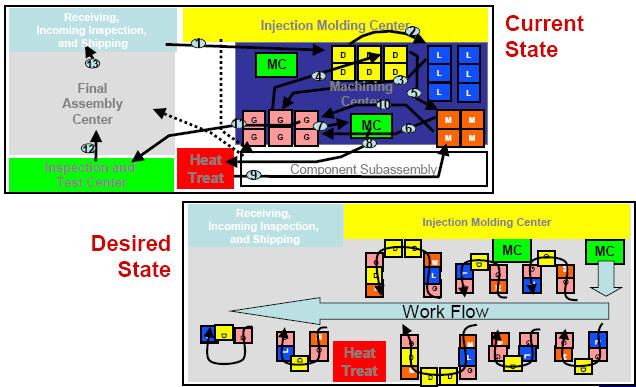
- Tính linh động: có khả năng sản xuất nhiều loại sản phẩm khác nhau một cách linh động hơn, chuyển đổi sản phẩm nhanh, thay đổi sản xuất nhanh …
- Tăng sản lượng: nếu có thể giảm chu kỳ sản xuất, tăng năng suất lao động, giảm thiểu ùn tắc và thời gian dừng máy, công ty có thể gia tăng sản lượng một cách đáng kể từ cơ sở vật chất hiện có.
- Hợp lý hóa tổng thể sản phẩm để loại bỏ những mẫu sản phẩm và biến thể ít mang lại giá trị tăng thêm cho khách hàng;
- Thiết kế những sản phẩm với ít thành phần hơn và phổ biến hơn;
- Thiết kế những sản phẩm và dịch vụ mà yêu cầu tùy biến của khách hàng có thể thực hiện được dựa trên những bộ phận và môđun được chuẩn hóa, và càng mới càng tốt.
Chỉ số OEE
OEE (overall equipment effectiveness) là thuật ngữ và là thông số rất phổ biến trong bảo trì năng suất toàn diện (Total Productive Maintenance).
OEE được dùng để đo lường hiệu quả hoạt động (effectiveness) của một thiết bị (equipment) một cách tổng thể (overall) thông qua cả 3 mặt nguồn lực– thời gian, chất lượng, và tốc độ vận hành – và qua đó giúp chỉ ra các vùng cơ hội để cải tiến.
OEE là chỉ số KPI chính để theo dõi trong hệ thống MES.
- Availability, tạm dịch là tỷ lệ hữa dụng, đo lượng tổn thất thời gian vận hành (downtime)
- Availability = (Thời gian hoạt động thực tế)/(Thời gian chạy máy theo kế hoạch) x 100%
- Quality, tạm dịch là tỷ lệ chất lượng, đo lượng tổn thất chất lượng
- Quality = (Tổng sản phẩm đạt chất lượng)/(Tổng sản phẩm sản xuất) x 100%
- Performance, tạm dịch là tỷ lệ hiệu suất, đo lượng tổn thất tốc độ vận hành
- Performance = (Tổng sản phẩm sản xuất)/(Thời gian chạy máy thực tế x công suất thiết kế) x 100%
OEE= Availability x Quality x Performance
Khi phân tích OEE, nhiều công ty có thể ngạc nhiên khi thấy rằng còn rất nhiều khả năng để tăng sản lượng trên từng thiết bị cụ thể. Chẳng hạn, công ty có thể giảm thiểu:
- Hỏng hóc thiết bị bất ngờ;
- Thời gian dừng do chuẩn bị và điều chỉnh thiết bị;
- Lãng công và ngưng chuyền do thiếu nguyên liệu, ùn tắc hay hoạch định sản xuất kém;
- Hoạt động thấp hơn tốc độ thiết kế do tay nghề công nhân kém, thiếu bảo trì hay các tác nhân khác;
- Khuyết tật trên sản phẩm cần gia công lại;
- Đo lường OEE rất có ích trong việc xác định các nguồn gây ách tắc, ra các quyết định đầu tư thiết bị và giám sát tính hiệu quả của các chương trình tăng năng suất thiết bị.
Các công cụ trong Lean
Xác định các lãng phí
Các loại lãng phí: để áp dụng các công cụ Lean một cách hiệu quả phải nh ận biết đuợc các loại lãng phí, các thao tác không mang lại giá trị cho khách hàng, từ đó lựa chọn công cụ thích hợp để loại bỏ lãng phí đã nhận biết.
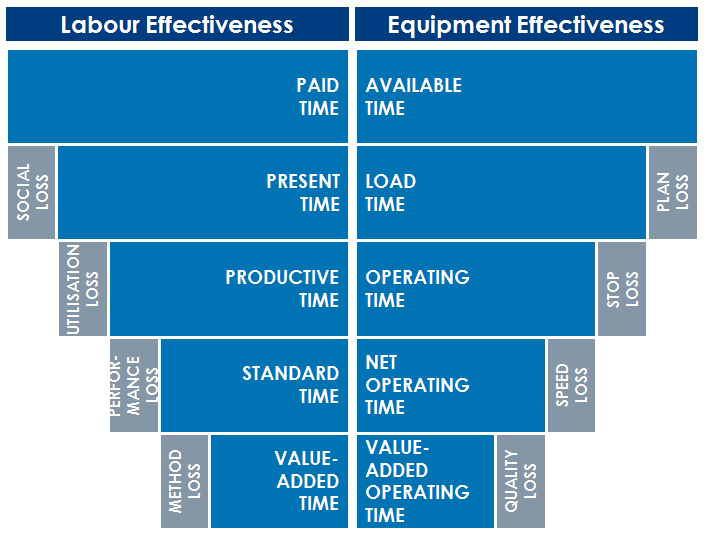
Dưới đây là một số loại lãng phí thường thấy
- Hàng sữa, hàng tái chế, phế phẩm: (Correction) :Sửa sai hay gia công lại, khi một việc phải được làm lại bởi vì nó không được làm đúng trong lần đầu tiên. Quá trình này không chỉ gây nên việc sử dụng lao động và thiết bị kém hiệu quả mà còn làm gián đoạn luồng sản xuất, dẫn đến những ách tắc và đình trệ trong quy trình. Ngoài ra, các vấn đề liên quan đến sửa chữ a thường tiêu tốn một khối lượng thờ i gian đáng kể của cấp quản lý, vì vậy làm tăng thêm chi phí quản lý sản xuất chung, ảnh hưởng đến hình ảnh công ty …
- Lãng phí do vận chuyển: (Transportation): Di chuyển ở đây nói đến bất kỳ sự chuyển động nguyên vật liệu nào không tạo ra giá trị tăng thêm cho sản phẩm chẳng h ạn như việc vận chuyển nguyên vật liệu giữa các công đoạn sản xuất. Việc di chuyển nguyên vật liệu giữ a các công đoạn sản xuất nên nhắm tới mô hình lý tưởng là sản phẩm đầu ra của một công đ oạn được sử d ụng tức thời bởi công đo ạn kế tiếp. Việc di chuyển giữ a các công đoạn xử lý làm kéo dài thời gian chu kỳ sản xuất, dẫn đến việc sử dụ ng lao động và mặt bằng kém hiệu quả và có thể gây nên những đình trệ trong sản xuất. Đây là loại lãng phí dài nhất.
- Lãng phí do chờ đợi (Waiting): Chờ đợi là thời gian công nhân hay máy móc nhàn rỗi bởi sự tắc nghẽn hay luồng sản xuất trong xưởng thiếu hiệu quả. Thời gian trì hoãn giữa mỗi đợt gia công chế biến sản phẩm cũng được tính đến. Việc chờ đợi làm tăng thêm chi phí đáng kể do chi phí nhân công và khấu hao trên từng đơn vị sản lượng bị tăng lên. Đây là loại lãng phí lâu nhất.
- Lãng phí do tồn kho (Inventory): Lãng phí về tồn kho nghĩa là dự trữ quá mức cần thiết về nguyên vật liệu, bán thành phẩm và thành phẩm. Lượng tồn kho phụ trội dẫn đến chi phí tài chính cao hơn về tồn kho, chi phí bảo quản cao hơn và tỷ lệ khuyết tật cao hơn.
- Lãng phí do thao tác (Motion): Bất kỳ các chuyển động tay chân hay việc đi lại không cần thiết của các công nhân không gắn liền với việc gia công sản phẩm. Chẳng hạn như việc đi lại khắp xưởng để tìm dụng cụ làm việc hay thậm chí các chuyển động cơ thể không cần thiết hay bất tiện do quy trình thao tác được thiết kế kém làm chậm tốc độ làm việc của công nhân. Đây là loại lãng phí nhiều nhất.
- Lãng phí do gia công thừa (Over-processing) : Gia công thừa tức tiến hành nhiều công việc gia công hơn mức khách hàng yêu cầu dưới hình thức chất lượng hay công năng của sản phẩm – ví dụ như đánh bóng hay làm láng thật kỹ những điểm trên sản phẩm mà khách hàng không yêu cầu và không quan tâm.
- Sản xuất dư thừa (Over-production) : tức sản xuất nhiều hơn hay quá sớm hơn những gì được yêu cầu một cách không cần thiết. Việc này làm gia tăng rủi ro sự lỗi thời của sản phẩm, tăng rủi ro về sản xuất sai chủng loại sản phẩm và có nhiều khả năng phải bán đi các sản phẩm này với giá chiết khấu hay bỏ đi dưới dạng phế liệu. Tuy nhiên, trong một số trường hợp thì lượng bán thành phẩm hay thành phẩm phụ trội được duy trì nhiều hơn một cách có chủ ý, kể cả trong những quy trình sản xuất được áp dụng Lean. Đây là loại lãng phí xấu nhất nó kéo theo các lãng phí khác.
Tiêu chuẩn hóa (Standard Work)
Chuẩn hóa quy trình có nghĩa là các quy trình và hướng dẫn sản xuất được quy định và truyền đạt rõ ràng đến mức hết sức chi tiết nhằm tránh sự thiếu nhất quán và giả định sai về cách thức thực hiện một công việc. Mục tiêu của việc chuẩn hóa là để các hoạt động sản xuất luôn được thực hiện theo một cách thống nhất, ngoại trừ trường hợp quy trình sản xuất được điều chỉnh một cách có chủ ý. Khi các thủ tục quy trình không được chuẩn hóa ở mức độ cao, các công nhân có thể có những ý nghĩ khác nhau về cách làm đúng cho một thủ tục quy trình và dễ đưa đến các giả định sai.
Mức độ chuẩn hóa cao về quy trình cũng giúp các công ty mở rộng sản xuất dễ dàng hơn nhờ tránh được những gián đoạn có thể gặp phải do thiếu các quy trình được chuẩn hóa. Thường áp dụng tiêu chuẩn cho một số công việc sau: Thời gian takt time (thời gian khách hàng yêu cầu), Lead time (Thời gian từ kho đến kho, thời gian từ công đoạn A đến công đoạn B). Mức tồn kho, số lượng, thời gian giao hàng, chủng loại, vị trí máy, cách vận hành máy, trình tự công việc…..
Chuyển đổi nhanh (Quick change over)
Là hoạt động rút ngắn thời gian chuẩn bị và chuyển đổi. Chuyển đổi được xem là kết thúc khi công đoạn được chuyển đổi ra hàng tốt đúng tiến độ. Các bước chuyển đổi nhanh: chuẩn bị nguyên vật liệu và dụng cụ, thay dụng cụ cũ bằng dụng cụ mới, chuẩn hóa và sắp xếp cho phù hợp dụng cụ cũ và mới. Phân công trách nhiệm rõ ràng, ai làm gì chuẩn bị gì.
5S và quản lý trực quan (5S and Visual Management)
Phương pháp 5S bao gồm một số các hướng dẫn về tổ chức nơi làm việc nhằm sắp xếp khu vực làm việc của công nhân và tối ưu hiệu quả công việc:
- Sàng lọc (Sort): phân loại những gì cần thiết và những gì không cần thiết để những thứ thường được cần đến luôn có sẵn gần kề và thật dễ tìm thấy. Những vật ít khi hay không cần dùng đến nên được chuyển đến nơi khác hay bỏ đi.
- Sắp xếp (Straighten/Set in order): sắp xếp những thứ cần thiết theo thứ tự để dễ lấy. Mục tiêu của yêu cầu này là giảm đến mức tối thiểu số thao tác mà công nhân thực hiện cho một công việc. Ví dụ, hộp công cụ cho công nhân hay nhân viên bảo trì có nhu cầu cần sử dụng nhiều công cụ khác nhau. Trong hộp công cụ, từng dụng cụ được xếp ở một nơi cố định để người sử dụng có thể nhanh chóng lấy được công cụ mình cần mà không mất thời gian tìm kiếm. Cách sắp xếp này cũng có thể giúp người sử dụng ngay lập tức biết được dụng cụ nào đã bị thất lạc. Định vị các vật di chuyển.
- ạch sẽ (Scrub/Shine): giữ các máy móc và khu vực làm việc sạch sẽ nhằm ngăn ngừa các vấn đề phát sinh do làm sạch kém. Trong một số ngành, bụi bẩn là một trong những tác nhân chính gây lỗi cho bề mặt hay nhiễm bẩn màu trên sản phẩm.
- Săn sóc (Stabilize/Standardize): đưa 3 công việc trên trở thành việc áp dụng thường xuyên bằng cách quy định rõ các thủ tục thực hiện các công việc sàng lọc, sắp xếp và giữ sạch sẽ.
- Sẵn sàng (Sustain): khuyến khích, truyền đạt và huấn luyện về 5S để biến việc áp dụng trở thành một phần văn hóa của công ty. Ngoài ra việc duy trì cũng bao gồm phân công trách nhiệm cho một nhóm giám sát việc tuân thủ các quy định về 5S.
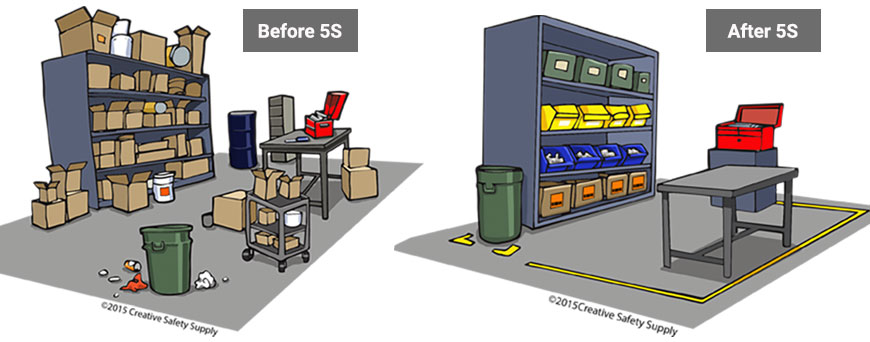
Các hệ thống quản lý bằng công cụ trực quan cho phép các công nhân của xưởng được thông tin đầy đủ về các quy trình sản xuất, tiến độ và các thông tin quan trọng khác giúp họ làm việc có hiệu quả nhất.
Xem thêm : Giám sát sản xuất với hệ thống ANDON System
Các bảng hiển thị lớn nói chung thường là công cụ thông tin hiệu quả hơn cho công nhân trong chuyền sản xuất so với các báo cáo và chỉ thị, nên được sử dụng càng nhiều càng tốt. Trong trường hợp cần cải thiện sự tuân thủ đối với một quy trình, việc trình bày trực quan giúp nhóm hiểu rõ hơn một quy trình phức tạp bao gồm các bước thao tác đúng, cách thực hiện đúng cho từng động tác, các mối quan hệ bên trong và bên ngoài giữa các hoạt động và với các tác nhân khác.
Các công cụ trực quan thường ở dưới các hình thức sau:
- Các bảng hiển thị trực quan: các biểu đồ, bảng đo lường hiệu quả, các thủ tục và tài liệu quy trình làm nguồn thông tin tham khảo cho công nhân. Ví dụ, biểu đồ xu hướng về hiệu suất thực hiện, % dao động của tỷ lệ lỗi, tiến độ xuất hàng trong tháng, v.v…
- Các bảng kiểm soát bằng trực quan: các chỉ số dùng để kiểm soát hay báo hiệu điều chỉnh cho thành viên nhóm. Các bảng biểu có thể bao gồm cả thông tin về tiến độ sản xuất, thông tin theo dõi chất lượng, v.v… Ví dụ các bảng màu chỉ thị giới hạn kiểm soát nhiệt độ hay tốc độ giúp người vận hành thiết bị nhanh chóng phát hiện khi quy trình vận hành vượt mức cho phép. Các thẻ Kanban là một ví dụ khác về kiểm soát bằng trực quan.
- Các chỉ dẫn bằng hình ảnh: công cụ này giúp truyền đạt các quy trình sản xuất hay luồng vật tư được quy định. Chẳng hạn, việc sử dụng các ô vẽ trên nền nhà xưởng để phân biệt khu vực chứa vật liệu sử dụng được với phế phẩm hay các chỉ dẫn luồng di chuyển nguyên vật liệu và bán thành phẩm trên mặt bằng xưởng.
Sơ Đồ Chuỗi Giá Trị (Value Stream Mapping)
Sơ đồ chuỗi giá trị là tập hợp các phương pháp giúp thể hiện trực quan luồng sản phẩm và thông tin qua quy trình sản xuất. Mục đích của phương pháp này là xác định các hoạt động làm tăng giá trị và các hoạt động không làm tăng giá trị.
Sơ đồ chuỗi giá trị mô tả dòng thông tin và dòng vật tư chạy trong nhà máy, phản ánh những gì đang thực sự diễn ra hơn là những gì được mong muốn xảy ra, nhờ đó các cơ hội cải tiến có thể được xác định. Sơ đồ chuỗi giá trị thường được sử dụng trong các dự án cải tiến thời gian chu kỳ quy trình vì nó thể hiện chính xác cách thức hoạt động của một quy trình với yêu cầu thời gian và từng bước công việc chi tiết. Phương pháp này cũng được dùng trong phân tích và cải tiến quy trình bằng cách xác định và loại trừ khoảng thời gian liên quan đến các hoạt động không tạo ra giá trị tăng thêm.
Kanban
“Kanban” là hệ thống cung cấp vật tư theo mô hình hệ thống kéo sử dụng các dấu hiệu tượng hình, như các thẻ treo phân biệt bằng màu sắc, để ra hiệu cho các khâu phía trước khi khâu sau cần thêm vật tư. Về tác dụng, Kanban là một công cụ thông tin hỗ trợ sản xuất theo mô hình hệ thống kéo. Một thẻ Kanban có thể là một thẻ treo, bảng hiển thị điện tử hay bất kỳ hình thức gợi nhắc trực quan nào thích hợp.
Có hai loại Kanban đặc trưng:
- Kanban Cung Cấp: một dấu hiệu từ khách hàng nội bộ đến nguồn cung cấp nội bộ cho biết loại vật tư cần được cung cấp.
- Kanban Tiêu Thụ: một dấu hiệu từ nơi cung cấp nội bộ đến khách hàng nội bộ cho biết rằng vật tư đã sẵn sàng cho việc sử dụng. Trong trường hợp này, nơi cung cấp nội bộ sẽ không sản xuất thêm cho đến khi việc tiêu thụ được thực hiện bởi khách hàng bên trong. Có nhiều biến thể trong hệ thống Kanban và trong thực tế có khá nhiều sách viết riêng về cách áp dụng Kanban hiệu quả nhất.
Cân Bằng Sản Xuất
Cân bằng sản xuất, hay điều độ sản xuất, nhắm tới việc bố trí lưu lượng sản xuất và chủng loại sản phẩm ổn định theo thời gian nhằm giảm thiểu sự đột biến trong khối lượng công việc. Bất kỳ sự thay đổi nào về lượng nên được cân bằng để chúng diễn ra từ từ với càng ít sự thay đổi đột ngột càng tốt. Điều này cho phép công ty tận dụng công suất sản xuất cao hơn đồng thời giảm thiểu việc chuyển đổi
mẫu mã sản phẩm. Yếu tố chính của cân bằng sản xuất đó là người chịu trách nhiệm ra lệnh sản xuất cho xưởng phải có một hệ thống tự động điều tiết các đơn hàng không để có sự đột biến về khối lượng sản xuất. Hệ thống này giúp việc phân bổ thiết bị và con người chính xác và dễ dàng hơn. Để áp dụng phương pháp này, công ty cần biết công suất thực và tốc độ thực hiện ở từng công đoạn sản xuất.
Sản xuất tinh gọn kết hợp sức mạnh của MES – MOM
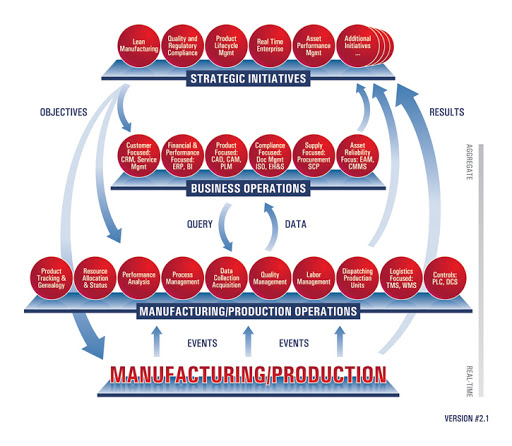
Giám sát sản xuất theo thời gian thực
MES – MOM cung cấp giải pháp giám sát thời gian thực của sản xuất.
Nó cũng cho phép nắm bắt và đủ điều kiện dữ liệu quản lý và cung cấp tất cả các yếu tố cần thiết cho sản xuất vận hành (tài liệu, kế hoạch, v.v.) một cách phù hợp và hiệu quả.
Để phương pháp Lean có hiệu quả, cần phải tuân theo các phép đo, theo dõi chúng trong khung thời gian dự kiến và có phân tích và kiểm soát dữ liệu sản xuất trong thời gian thực. Tần suất thu thập dữ liệu được cho phép bởi một công cụ MES – MOM sẽ tăng hiệu quả và giải quyết vấn đề nhanh chóng.
Thiết lập các chỉ số đáng tin cậy và hiệu quả
Một công cụ MES – MOM bổ sung cho cách tiếp cận Lean bằng cách hỗ trợ nó, củng cố nó và thực hiện các thực tiễn tốt nhất, đo lường hiệu suất và cải thiện quy trình bằng cách loại bỏ lãng phí . Nó sẽ đảm bảo sự thành công của một phương pháp cải tiến liên tục bằng cách đẩy nhanh các sáng kiến Sản xuất tinh gọn.
Để thực hiện một cách tiếp cận Lean hiệu quả, cần có dữ liệu đáng tin cậy được thu thập và đo lường chính xác. Đó là lý do tại sao một công cụ MES – MOM rất quan trọng. Thu thập dữ liệu thủ công hiếm khi hiệu quả.
Hỗ trợ cho các thành phần khác nhau của Sản xuất tinh gọn
Một triển khai chung cũng sẽ giúp có thể thực hiện các bước khác nhau của Sản xuất tinh gọn (tính toán và theo dõi phương pháp OEE, 5S, Sigma, Smed, v.v.).
Bằng cách lập kế hoạch cho các giai đoạn khác nhau của giảm lãng phí , giảm chi phí và quản lý chất lượng, các quy trình có thể được thực hiện ngay lập tức theo cách mạch lạc, và trên hết, được duy trì theo thời gian.
Các khu vực để cải tiến có thể được xác định rõ ràng từ máy này sang máy khác, từ xưởng này sang xưởng khác và từ nhà máy này sang nhà máy khác bằng cách giám sát các hoạt động và thiết lập các chỉ số hiệu suất chính (KPI) .
Hỗ trợ quản lý thay đổi (change management)
Cuối cùng, một công cụ MES – MOM , bằng cách tự động hóa việc cải tiến quy trình, sẽ giúp quản lý thay đổi và áp dụng nó dần dần cho đến khi nhận được sự hỗ trợ của nhân viên. Người vận hành được thông báo trong thời gian thực về bất kỳ trục trặc nào và có thể phản ứng ngay lập tức: Sau đó, họ đang ở trong một vị trí để có hành động khắc phục thích hợp.
Theo cách tương tự, trong bối cảnh hiện nay, các công ty phải chú ý nhiều hơn đến hậu quả môi trường của các quy trình được sử dụng, các sản phẩm và dịch vụ được cung cấp, trong đó chi phí năng lượng và giá vật liệu không ngừng tăng lên, nhà sản xuất phải áp dụng hiệu quả chiến lược phát triển bền vững: cách tiếp cận Lean kết hợp với công cụ MES – MOM sẽ cho phép nhà sản xuất duy trì tính cạnh tranh.
Kết luận
MES – MOM và Lean bổ sung lẫn nhau và không độc lập như một số người đưa ra. Một công cụ MES – MOM sau đó sẽ đóng một vai trò quan trọng trong sự thành công của quy trình Sản xuất tinh gọn. Với mục tiêu Đảm bảo cải tiến liên tục, giảm lãng phí và cải thiện thời gian phản hồi, một công cụ MES – MOM chắc chắn sẽ tăng thêm giá trị: tiết kiệm thời gian, tăng tài nguyên để duy trì và tối ưu hóa hiệu suất hoạt động trong công ty.